June 24, 2019
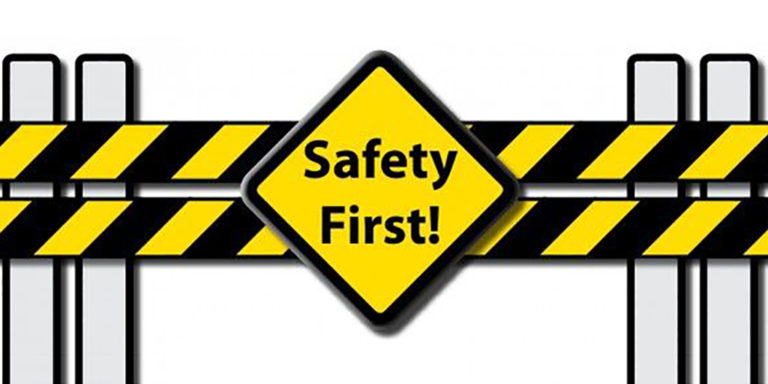
Safety First: Best Practices for Gasket Installation and Maintenance
When it comes to industrial safety, every detail matters—especially when working with bolted flange joints. At the heart of a secure seal lies the gasket, and ensuring it’s correctly selected, installed, and maintained is crucial for avoiding leaks, equipment damage, and serious injuries.
Qualified Installers and Proper PPE
The first step in safe gasket installation is using a qualified assembler, trained according to ASME PCC-1 guidelines. Safety doesn’t stop there—always wear appropriate personal protective equipment (PPE) such as safety glasses, gloves, steel-toe boots, and hard hats. Additionally, always follow lockout/tag-out procedures to ensure the system is depressurized and safe to work on.
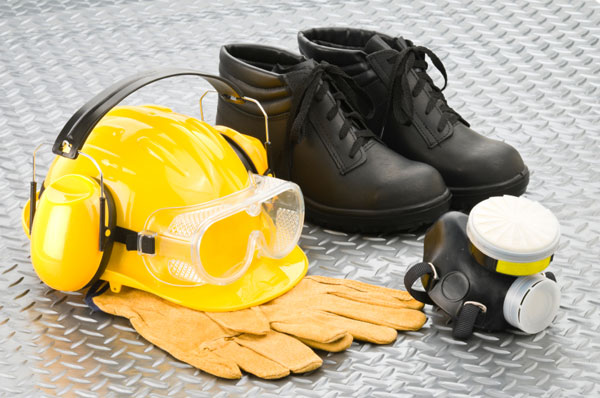
Gasket Selection: More Than Just Size
Choosing the right gasket involves more than fitting—it’s about compatibility. Key factors to consider include:
Understanding stress variables such as minimum seating stress, ideal operating stress, and maximum allowable stress is essential. Using a gasket made from incompatible material can lead to premature deterioration, leaks, and serious risks.
Installation: No Shortcuts Allowed
Never reuse a gasket. Once compressed, its mechanical properties change, reducing its ability to seal properly. During installation, ensure surfaces are clean and free from debris, and follow approved bolting patterns—such as the star pattern detailed in ASME PCC-1.
Improper torque, uneven load, or exceeding the gasket’s temperature limits can result in blistering, heat cracks, or leakage. A well-followed bolting procedure is the foundation of a safe, long-lasting seal.
Safe Disassembly Procedures
Disassembling a joint requires just as much caution. Make sure:
Ask yourself critical safety questions before starting disassembly—Is there pressure? Fluid? Could the system shift or load swing? Being prepared is key to avoiding injury.
Preventing Leaks with Proper Load Management
The most common cause of gasket leaks is gasket unloading due to insufficient seating stress. This often stems from improper bolting or friction unaccounted for during tightening.
The solution? Follow a consistent bolting procedure, like the one outlined in ASME PCC-1.
For help with specific applications or general procedures,contact our application engineers at tech@durlon.com and download our Bolt Tightening Worksheet to ensure every seal is a safe one.